Directional Boring
Directional boring, commonly called horizontal directional drilling or HDD, is a steerable trenchless method of installing underground pipes, conduits and cables in a shallow arc along a prescribed bore path by using a surface launched drilling rig, with minimal impact on the surrounding area.
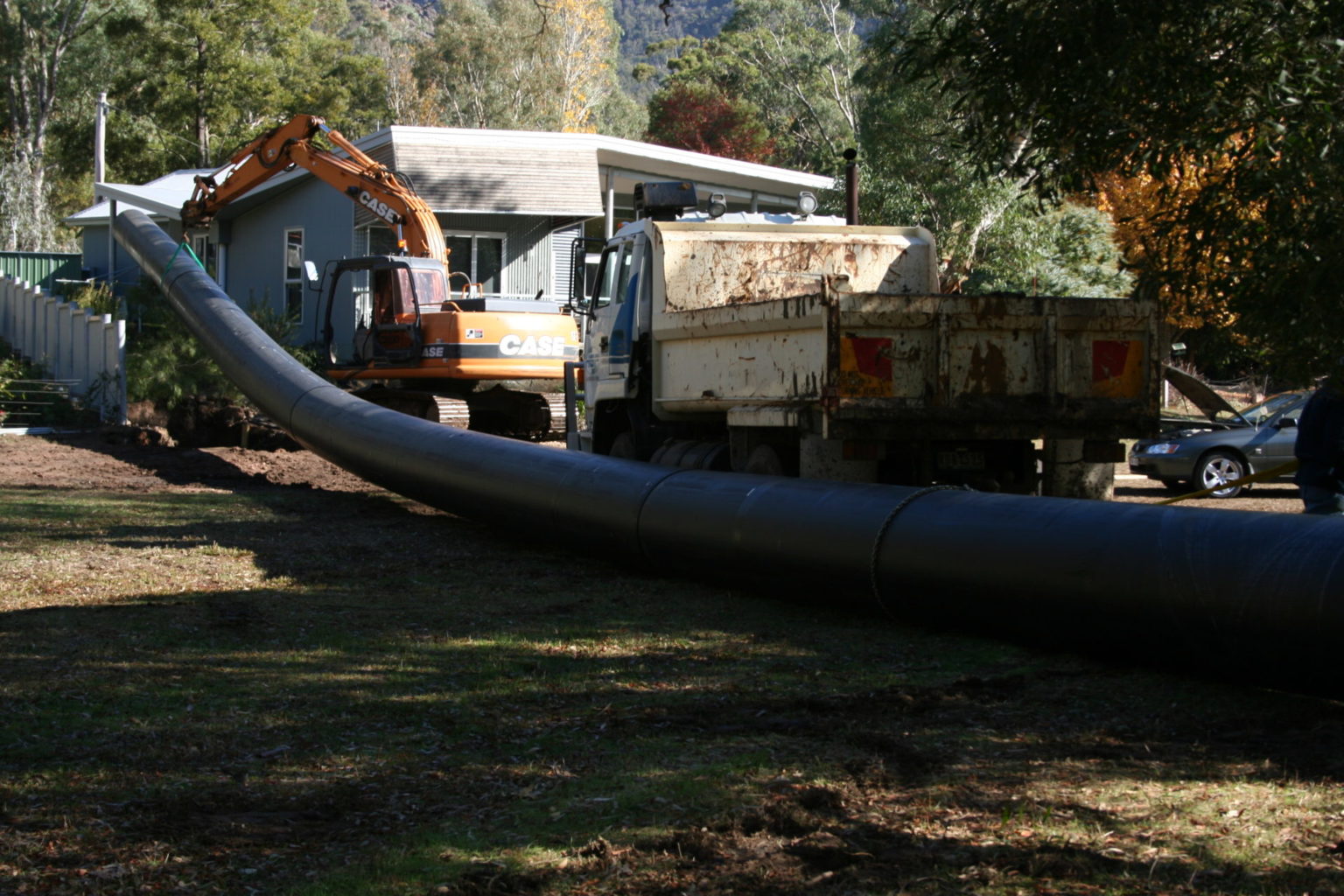
Directional Boring
Directional boring, commonly called horizontal directional drilling or HDD, is a steerable trenchless method of installing underground pipes, conduits and cables in a shallow arc along a prescribed bore path by using a surface launched drilling rig, with minimal impact on the surrounding area.
Directional boring is used when trenching or excavating is not practical. It is suitable for a variety of soil conditions and jobs including road, landscape and river crossings. Installation lengths up to 200m have been completed, and diameters up to 56" (1,200mm) have been installed in shorter runs. Pipes can be made of materials such as PVC, polyethylene, polypropylene, Ductile iron, and steel if the pipes can be pulled through the drilled hole.
Directional boring is used for installing infrastructure such as telecommunications and power cable conduits, water lines, sewer lines, gas lines, oil lines, product pipelines, and environmental remediation casings. It is used for crossing waterways, roadways, shore approaches, congested areas, environmentally sensitive areas, and areas where other methods are costly. It is used instead of other techniques to provide less traffic disruption, lower cost, deeper and/or longer installation, no access pit, shorter completion times, directional capabilities, and environmental safety.
Our Process
The process starts with receiving hole and entrance pits. These pits will allow the drilling fluid to be collected and reclaimed to reduce costs and prevent waste. The first stage drills a pilot hole on the designed path, and the second stage enlarges the hole by passing a larger cutting tool known as the back reamer. The reamer's diameter depends on the size of the pipe. The driller increases the diameter according to the material being cut and to achieve optimal production. The third stage places the product or casing pipe in the enlarged hole by way of the drill steel; it is pulled behind the reamer to allow centering of the pipe in the newly reamed path.